Radial stays ahead of the automation curve
In one of its Louisville fulfillment centers, Radial has combined conventional automation for picking with a robotic putwall for order assembly. The goal: demonstrate leadership in automation to improve productivity
No one questions whether warehousing and distribution is in the midst of an automation boom. The last decade or so witnessed the introduction of goods-to-person picking technologies like shuttles; autonomous mobile robots for robots-to-goods picking; and now technologies for autonomous lift trucks and robotic trailer unloading.
Then you havepiece-picking robots, which hold the promise of automating the most labor-intensive processes in any facility—those that involve a person picking items to and from a tote.
Take an inside look into the systems in place in the new Radial facility here.
Although robotic piece-picking has been slow to gain broad traction, robotic putwalls are generating steam especially from forward-thinking companies looking to get ahead of the technology curve. Those companies recognize that emerging technologies will improve over time; the winners will be the early adopters who were patient enough to understand the limitations and strengths.
One of those companies isRadial, athird-party logistics (3PL)provider that is part of bpost group, Belgium’s leading postal operator, and a fast-growing parcel and omni-commerce logistics partner in Europe, North America and Asia.
Working withCovariant, Radial has installed 12 AI-powered robotic putwalls in a 500,000-square-foot, single-client facility in Louisville, Ky., that handles the e-commerce fulfillment of health and beauty products. The facility ships 20,000 parcels per day, with capacity to ship up to 50,000 parcels per day during peak season.
Each of the robotic putwalls (the facility also uses manual putwalls) can pick between 450 to 500 picks per hour, or up to 100,000 units per putwall per month for a total of 1.2 million units per month.
The robots are accomplishing two of Radial’s overarching goals, according toChris Epley, the site director. One is to provide a new tool to balance the reliance on labor that every fulfillment center is facing.
A side benefit is that robots are creating the opportunity to upskill some of the workforce through the creation of new and more elevated positions as bot tenders, or individuals who monitor the robots rather than manually pick items.
Caption: In Louisville, Radial is using piece handling robots as part of a robotic putwall to assemble orders. The robots can handle 100% of Radial’s SKUs and are constantly improving.
“We have people in the facility who are very excited about the technology and are embracing it,” Epley says.
The second goal is that in a very competitive space, the adoption of automation, including robotics, positions Radial as a thought leader.
“Our clients are looking for a partner that is flexible in the solutions we offer, that can ramp up and ramp down according to demand, and control costs,” says Epley. “Radial is dedicated to identifying automation strategies we can deploy to meet our clients’ business needs and be more aggressive in the space.”
New organization, 35-year history
Thee-commerce物流供应商现在被称为径向被收购d by bpost in 2017. The company has decades of experience in e-commerce fulfillment.
Founded in 1995 as GSI, it specialized in sporting goods and supplies. By 2011, when the company was acquired by eBay for approximately $2.4 billion, it was a leading provider of fulfillment services. A 2016 merger with Innotrac led to the creation of Radial. Today, Radial has a global footprint that includes 28 facilities in the United States and serves customers as diverse as Gymshark and Puma. While the company’s focus is e-commerce fulfillment, Radial also offers wholesale and store replenishment for some customers.
Robotic putwalls are not the only flexible automation Radial is adopting in its facilities. Although not being used in this Louisville site, Radial has implemented autonomous mobile robots from Locus and Exotec’s Skypod. Radial is also recognized as a leader in the distributed order management, or DOM, space.
The move to automation is being driven by customers seeking more agility and flexibility in their solutions. “We have been staying ahead of the curve in the implementation of automation,” says Epley. “We have multiplewarehouse management system (WMS)platforms, warehouse execution systems (WES) and warehouse control systems (WCS) as well as voice technology, and now we’re exploring robotics.”
Epley adds that Radial’s solutions team scouts for innovation and automation that can be leveraged across multiple clients and multiple buildings. Locus, for instance, is being used in at least four facilities. “One of the reasons we’re partnering with Covariant is that the solution was viable for this site, but also has the potential to be used across multiple clients in other buildings,” Epley says.
Caption: Items are picked to tote and then conveyed to the robots. Once a cubby is order complete, a packer prepares it for shipping.
This building is a single client fulfillment center that has been in operation with its current tenant since 2010. It began as a relatively small, manual pick and pack operation. In 2013, Radial purchased the building next door and connected the two to add more square footage. That year, it also invested in conveyor automation, a shipping sorter, multi-level pick modules and automated print-and-apply technology.
With the pick modules, the building transitioned to 100% batch picking; totes were picked complete in a zone in the pick modules and then conveyed to a manual putwall area for order consolidation.
That remained the status quo until around 2019. “Over the last few years, and especially during Covid, demand for this client increased dramatically,” says Epley. “The ramp up for peak went from a factor of 1 to 3 to a factor of 1 to 5. We began the search for a solution that would not only address the labor challenges in Louisville, but allow us to get staff trained and up to speed very quickly during peak.”
Why an automated putwall versus another process? Two reasons, according to Epley. One was the limitation of the building layout: For instance, integrating autonomous mobile robots into a multi-level pick module would have required significant physical changes.
“We have a high volume of pick from pallet,” Epley says. “That would’ve required a massive layout change.” And second, the facility already had a space designated for manual putwalls. If the technology worked, it was a natural transition.
Caption: Packing materials are staged for use.
Bringing in robotics
Parent company bpost group was already partnering with Covariant’s robotic putwalls in Europe. It was an existing part of bpost group’s technology stack, and the two organizations had a working relationship.
The project got underway in the spring of 2021 with a very aggressive timeframe. The first step, according to Epley, was to conduct a proof of concept in Louisville. “This site is one of our more mature and established sites, so it is often used as a laboratory for new initiatives,” Epley says. “Working with the team from Covariant, we worked to address questions such as: What is the process for the manual putwalls? How do they integrate with the WMS? And, how are exceptions going to be handled? The first test robot was installed in the third quarter of 2021.”
During the early weeks of testing, the robot didn’t run live batches of orders. Rather, Radial provided Covariant a large array of its client’s products, which range from candles to body creams, so Covariant could benchmark performance levels and train the robot to pick or sort new items that Covariant’s software had not yet experienced.
“The client has a relatively low number of SKUs but a high variance of package sizes, shapes and forms, and the label placement is different across every SKU,” Epley notes.
在概念证明早期的经验之一was that there were few items the robot struggled to grasp; Epley estimates the robots are picking 100% of the SKUs. The challenge was learning to put items into a cubby given the variation in packaging forms and sizes.
“As with any new solution, we knew we would have challenges,” Epley says. “Sometimes, the robot couldn’t hold on to an item long enough to sort it into a cubby; sometimes there was mis-sorting into the wrong cubby. There were also challenges around the speed of the robot as it was learning to handle all the SKUs.”
In early November, the project was put on temporary hold to focus on the holiday season.
Getting it right
While Radial concentrated on the holiday season with manual putwalls, Covariant worked behind the scenes to improve picking and putting. In January 2022, the pilot resumed, with Radial allocating up to 60 days to “get it right and sign off on the technology,” according to Epley.
在那段时期,从Covaria工程团队nt and Radial worked together to increase the picking speeds and accuracy on the pilot robot to a point that could justify moving the project forward. By the end of February, Radial was ready to proceed with an eye toward the 2022 peak holiday season.
By November 2022, 12 robotic putwalls were in place, with each putwall capable of handling 100,000 units per month. The putwalls are U-shaped and have either 96 or 120 cubbies, depending on how the cubbies are sized. The robotic system is at a point where “we only use manual putwalls if demand requires it, such as during peak,” says Epley.
One of the takeaways is that even with the ability to pick nearly 100% of the items in the facility, there will still be the occasional mis-pick or mis-sort. In addition, the robot might stop for safety reasons if it can’t read a bar code or if there is a problem with a photo eye. That, in turn, has created a new, higher skilled position in the facility, the bot tender. This individual monitors the robots from a user interface on a table associated with each robot. The development of the tablet interface was a special implementation to better guarantee that facility performance metrics are met by the robots.
The bot tender ensures each bot has all of the totes assigned to a batch that is about to be sorted. When a robot encounters an item it can’t pick, for whatever reason, it’s placed in a separate exception bin. The bot tender is notified on the tablet to manually sort those items.
“Our ultimate goal is bot throughput, and we are still in the process of growing into the technology,” Epley says. As a result, Radial is operating with one bot tender to two robots. The goal is to get to one bot tender to four robots, or a total of three bot tenders. “We still have a ways to go, but we have a path to get there,” Epley says.
He also notes that the robots have been embraced by the workforce at the facility. “When we get new associates in the door, one of the first things the experienced associates do is take them to see the robots,” Epley says.
When asked what advice he would offer to a colleague considering an emerging technology for their facility, Epley says, “first and foremost, be patient and be flexible. No solution comes without its challenges.” That goes double for emerging technologies. After working with the robots for nearly a year, Epley believes the adoption of next-generation technologies is crucial to meet the demands of today’s customers while also addressing the inherent labor challenges in logistics hubs like Louisville, where e-commerce warehouses are clustered near parcel shipping depots.
Just as importantly, emerging technologies set Radial apart from its competitors. “If you’re a new client coming into this building, you’ll see that we’re innovative,” Epley says. “The market is ever-changing, and if we’re not in front of the curve, we’ll be at the back. I’m excited by where we’re at, and where we’re going.
What's Related in Robotics
Related Topics
Covariant Inventory & Picking Locus Robotics piece picking robots Robotics All topics


Image Courtesy of Covariant
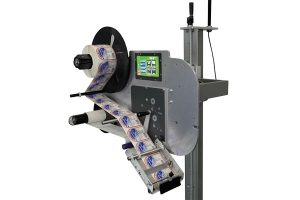
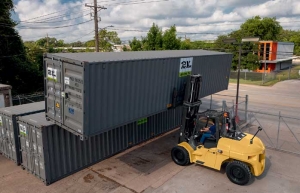
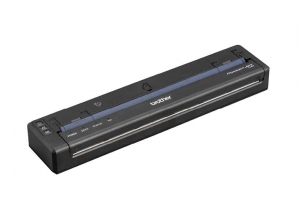
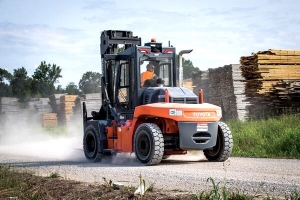